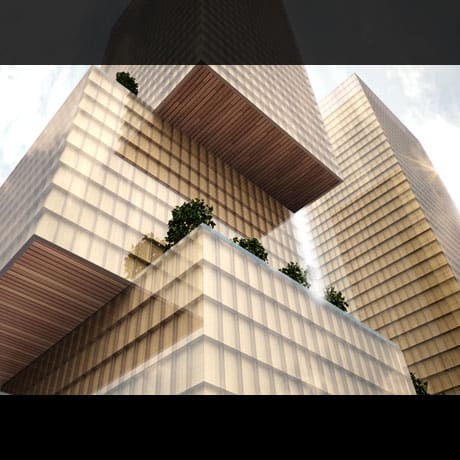
The color black – simple. Right?
In the world of print the color black is anything but simple. There are points that should be understood when putting black ink on paper. Read on to find out more about the whys and hows of black ink.
Process Color / CMYK
The problem of black ink is rooted in color theory. That’s boring though so let’s skip ahead.
The colors of Cyan, Magenta and Yellow when combined should arrive at the color black. In the real world though they add up to a muddy brown. And even if 100% CMY equalled black we would be stuck with 300% total ink density and the resulting drying issues.
So CMY loads up the ink while not making black. Thanks CMY. Then how can we cut total ink density and arrive at a true black? You guessed it – use black ink (the ‘K’ in CMYK).
Black, black or black?
Ok, great – now we know that we need to use black ink. But how much should we use, when should we use it and what new problems do we introduce?
In the case of photos, design software or the RIP will take care of blending in the proper amount of black when needed. That leaves us to only worry about objects and text. In both cases we need to understand the difference between different definitions of black. Namely; Black, Rich Black and Registration Black.
Black, Rich Black, Registration Black
Registration Black is easy so let’s get it out of the way first. Don’t use it. Ever. Seriously.
Its only purpose is so that printer’s marks can appear on all printing plates regardless of what separation the plate represents. If you’re responsible for press imposition then you already know everything that this article will discuss. Thanks for checking it out but stop reading and go impose something. The rest of us can keep reading.
With Registration Black out of the way we only have to worry about Black and Rich Black.
Rich Black is no more than black ink reinforced with percentages of the other colors being used to print your multi-color product. For instance, if we are using CMYK (process color), in the areas that are to appear black we will add some cyan, magenta and yellow behind the black ink. If you look at the photo above, the black bar at the top is representative of overprinting a solid bar of black ink on top of the image. See how the image tends to show through the black? Where the image is darker so is the black bar. And the lighter areas still look black but not really black.
At the bottom of the photo, the black bar isn’t overprinting the photo, it is a solid object with a Rich Black build. There’s no chalky gray or image show through. It’s just black. But only because it’s not just black, it’s Rich Black.
The other colors combine to produce a medium gray on which we printed solid black. That’s the magic of Rich Black – we are printing all four colors to achieve a deep, dense black color but we are keeping our total ink density to a manageable level. Take that CMY.
When to Use: Photo effects, CMYK printing, large areas
So here it is. Rich black can, and often should be used for large solid areas of black when using process color. It can also be used to match the hue of black in a photo for something like a photo border.
Have you ever noticed that B&W photos in color books, instead of appearing a neutral gray often appear either cool or warm? Remember, your B&W photos are being printed with CMYK. Too much cyan or magenta density in the mix can color shift your grays.
This can be used to great effect when done intentionally. If you have a B&W photo of a desert sunset you can add a little Magenta to the curve to give the photo a warmer tone. Or a little Cyan can be added to a winter scene. It will still appear B&W but will add a subtle suggestion to the viewer about the image.
When not to use: Neutral B&W photos, small type or logos, spot color jobs
It’s tempting then to used Rich Black everywhere. But just because you can doesn’t mean you should.
Take for instance lowly 10pt black text. If we used Rich Black here the Pressman would say very bad words. That’s because he now has to try and hold perfect registration across the entire press sheet. And there’s no such thing as perfect registration. The least little bit of misregistration will be obvious to the naked eye. The text will look blurry and difficult to read. The same is true for fine details in knockout areas – white text on a solid black area for instance. Or fine details in a multi-color logo.
Neutral B&W photos almost always look better when printed with black ink alone. Registration is less of an issue here but another printing press reality comes into play. Ink density and coverage can work against each other on the press sheet. In a heavy coverage area we have to increase the delivery of some inks. If your B&W photo is using Rich Black, it can color shift as described above. Adjusting for this then can throw off other elements on the sheet.
In these cases the advantages of Rich Black are outweighed by practical issues. Some of which can be overcome with trapping but that’s something for prepress to sort out. The layout artist is better off using straight black to avoid printing themselves into a corner.
As a general rule Rich Black should not be used when printing with spot colors. Spot colors are rarely a neutral color so they will color shift your black. And even if this is the desired effect, spot colors are more opaque than process color inks. You won’t know what you’re getting until it’s too late. For instance. you might be trying for a slightly blue cast Rich Black by adding some of that Reflex Blue into the mix. Won’t you be disappointed when it ends up being a deep purple instead.
What build? (hint: 55 / 44 / 41 / 100)
Warnings aside, you’re stoked to use Rich Black on your next project. Awesome. But how much is too much and what’s not enough?
Ask several prepress operators what build to use and I guarantee you will receive a different answer from each. There is no industry standard to follow and often these builds are bourn from experience in their own shop with their own particular mix of equipment and materials. The goal is to find a balance between the CMY build that results in a medium gray. One that’s strong enough to reinforce black ink but is light enough to keep your total ink density in check.
The build that works for me in most cases is 55% cyan, 44% magenta, 41% yellow and 100% black. This will give you 240% total ink, produces a very neutral gray in the event that you use transparency effects in your design and will still arrive at a solid Rich Black.
Rich Black for the Win!
The color Black is a little more involved than it seems up front. With this knowledge though you can now avoid some pitfalls and punch up the density of black on your final printed piece.
Our pre-press experts are an indispensable resource available to you on any project. We are only a phone call or an email away: 770-664-8199 / prepress@advancedpf.com.